Advice from the CCAA. New South Wales has over 300 active concrete batching plants that produce numerous concrete by-products and wastes. The NSW legislation and regulations require that all operators remain committed to minimising the amount of new resources used during the production process, to ensure that as much material as possible is recycled or re-used, and any waste which cannot be re-used is disposed of appropriately and ethically.
More often than not, many concrete by-products can be re-used in the concrete batching process without breaching any of the existing environmental regulations. The CCAA has developed a document to provide guidance on the regulatory requirements for managing the four main concrete by-products. These products are specifically known as:
Concrete By-Product | Definition |
1. Hardened Returned Concrete | Hardened Returned Concrete is concrete that has been returned to a concrete plant and has been cured and hardened. Hardened Returned Concrete contains the same properties as normal concrete and is largely free of contaminants, such as wood, cementitious materials, paper, steel reinforcement, plastic and brick. Once hardened, this concrete can be handled and stored with little risk of contaminated water runoff. |
2. Concrete Wash Water | Concrete Wash Water has a high pH (near 12), which makes it highly alkaline, and it also has an excessive matter of suspended solids. Concrete Wash Water is the product produced from washing pumps, trucks, chutes and mixers or simply cleaning out and agitator bowl and hosing down the batch plant yard. |
3. Liquid Wash / Slurry | Liquid Wash Out is an unavoidable by-product of the concrete batching. The washout slurry descends to the bottom of settling ponds and tanks in concrete plants which makes it extremely challenging to pump and transfer. It is also an alkaline material which is exceptionally difficult to re-use in the concrete batching process as it is not a consistent product and it re-use presents numerous concrete performance and technical issues. |
4. Solid Wash Out | Solid Wash Out has the consistency of clay and is returned concrete that has been washed out and dried. It is a mixture of sand and aggregates from the original concrete, and contains hydrated lime and other cementitious materials which sources alkalinity. This material is generally taken out of washout pits, drained, dried, transported to quarries or recycling centres and recuperated for re-use. |
Ref: Extracted from the NSW Government’s Concrete by-product Recycling and Disposal Industry Guidelines
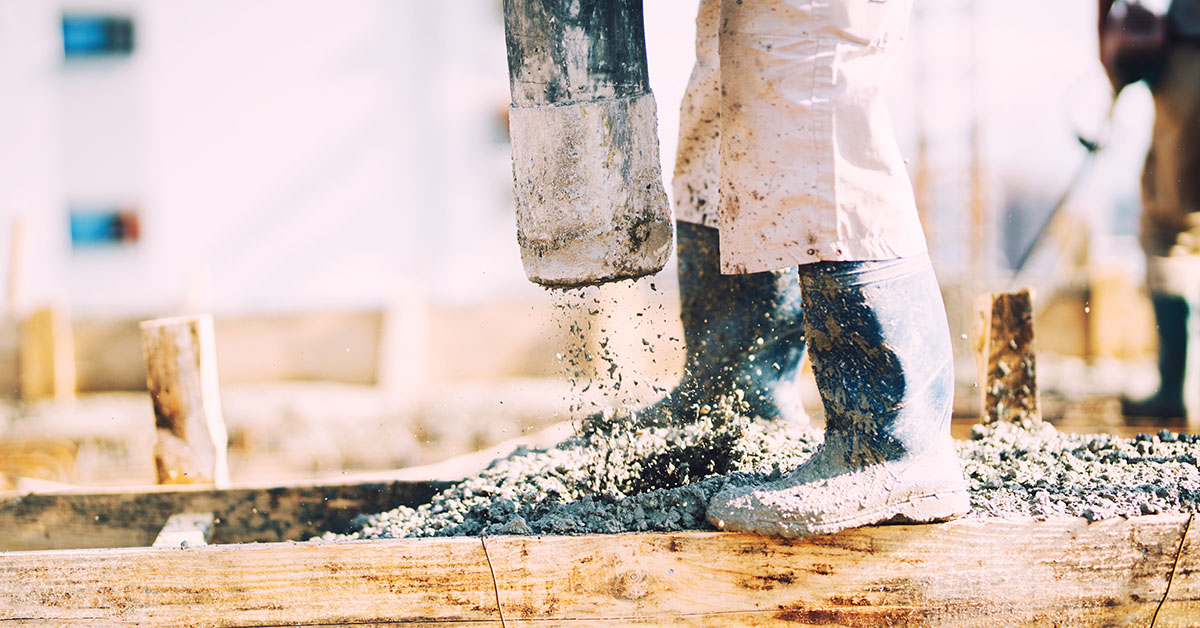
How to Deal with Different Types of Concrete By-Product
1. HARDENED RETURNED CONCRETE General Exemptions Re-use
Hardened Returned Concrete can be crushed at facilities that have the applicable licences to form recovered aggregates. In this manner it can re-used in the concrete batching process, or applied to the land as engineering fill or as road base.
This material can be applied to road construction on private land if the following conditions are met:
- Development consent for the development has been approved under the appropriate Environmental Planning Instrument.
- The relevant waste is applied to land at the smallest degree necessary for the construction of a road.
- It is to provide access (permanent or temporary) to a development approved by a local government.
The material being applied to the land must be sampled and tested, to ensure that it will pose marginal threat or harm to the environment.
Hardened Returned Concrete cannot be utilised for the following applications:
- Quarry, mine and sand dredge rehabilitation
- Dams
- Back fill for voids
- Utilised in reshaping land for agricultural purposes.
2. CONCRETE WASH WATER Re-use and Recycle
Concrete Wash Water is generally stored on-site at a concrete batch plant in settling ponds and is recycled into the concrete batching system. This process is advisable as it also reduces the requirement for clean mains water in the concrete batching process.
3. LIQUID WASH OUT / SLURRY Liquid Wash Out is categorized as liquid waste material. As such, this waste is required to be transported by licensed contractors in specialized “sucker trucks”, designed for this task specific task, and disposed of at licenced facilities.
Re-use and Recycle
Liquid Wash Out can be stored in settling ponds, which are stressed to keep the material in a state of suspension. The Liquid Wash Out or Slurry is maintained as such, in its liquid state. The water can then be pumped out and recycled back into the batching process, whilst leaving the majority of the cementitious alkalinity material in the settling pond.
Disposal
If Liquid Wash Out cannot be kept in a state of suspension, the material will collect at the bottom of the settling pond, requiring it to be pumped out and disposed of at a licensed facility.
Transform
The final option for dealing with Liquid Wash Out is to change it from liquid waste into solid waste. This is an advisable process as it;
- increases the number of disposal sites licensed to accept the waste
- increases the ease of handling the waste
- decreases transport costs and disposal fees.
One procedure applied for transforming the waste from a liquid to a solid, is to pump the slurry into dewatering tubes for geofabric bags.
4. SOLID WASH OUT Disposal
Solid Wash Out does not require a licensed transported and does not entail tracking. Nonetheless, if the material is to be disposed of, it needs to be transported to a licensed facility. At the licensed facility, Solid Wash Out is either re-processed into sand and gravel, it is mixed with various other materials to either fill another product or become road-base.
If you are interested in optimising the way you deal with different types of concrete washout, get in contact with one of our experts for a more efficient and environmentally friendly solution at 1300 366 668 or by using the PumperDump App (App Store) (Google Play)
Ref: Extracted from the NSW Government’s Concrete by-product Recycling and Disposal Industry Guidelines